Cosplayers
Crafting Cosplay Armor: Materials and Prop Construction Tips
4 mins read
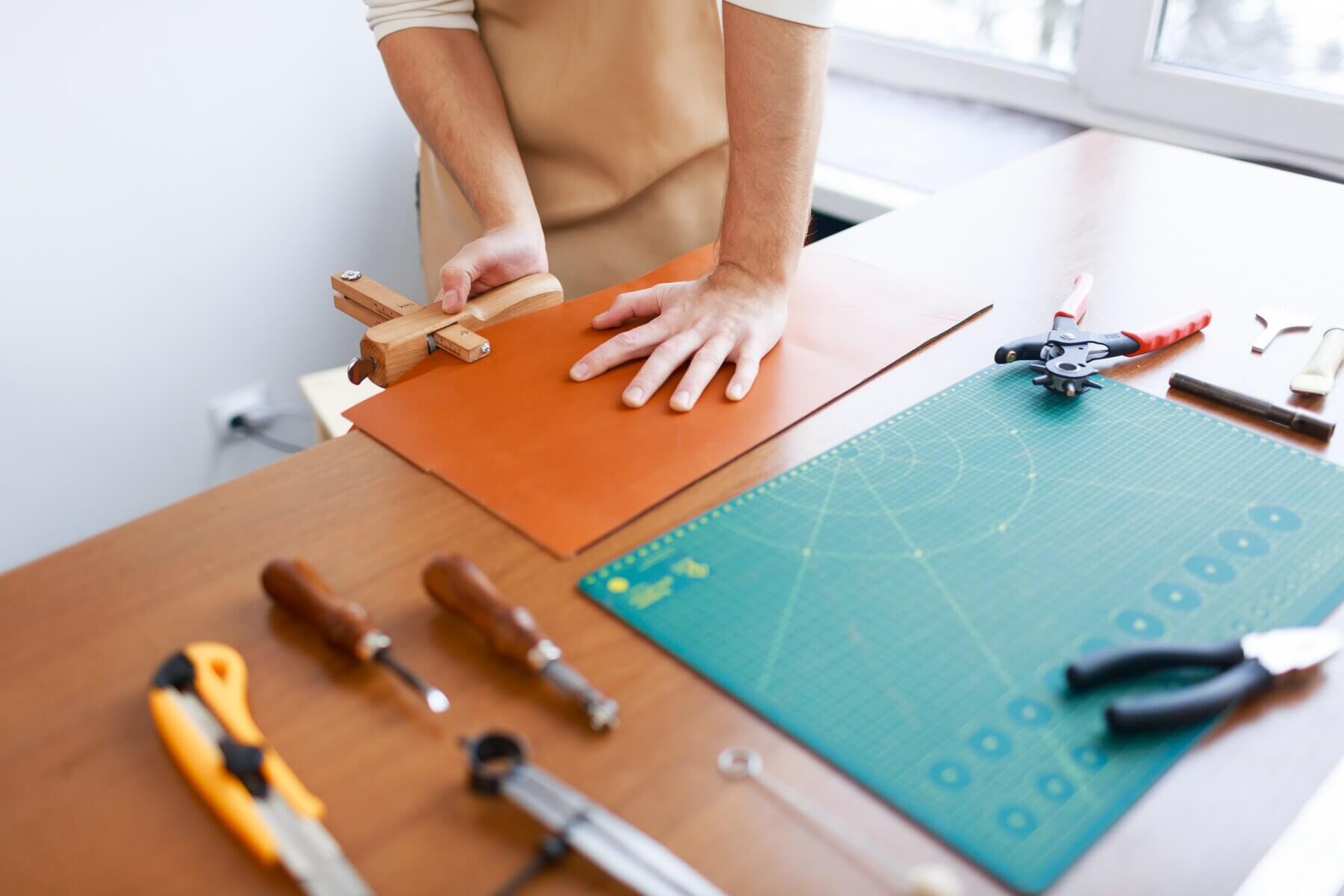
One of the biggest challenges that cosplayers face is the creation of the whole costume set itself. It takes a lot of planning and preparation, as well as investment for the equipment and materials. There’s also the matter of knowing HOW to work with certain materials, especially if you’re not yet familiar with their flexibility and durability, which are two very important aspects when it comes to material-selection and creation method-planning. You also need to worry about the “wearing” part–if you can move around and pose in the armor, holding the props and maintaining character. In order to help you out, here are some helpful tips.
1. Plan out your costume creation process
Before diving into the crafting process, it’s important to have a clear idea of what your finished product would look like. Do a quick Google search of your character; focus on finding high-resolution images, concept art, and screenshots of the characters’ armor, weapons, and props, preferably from multiple angles. Take note of how you’ll scale your measurements with the character’s measurements. Through this, you’ll have a clear foundation you can anchor yourself in, and you’ll avoid spending time and resources on repetitions.
Selecting the right materials and securing the right equipment are also big parts of your planning stage. Some of the usual materials in cosplay creation are EVA foam, thermoplastics, and even 3D printing. Get to know the characteristics of each material, then match it with the equipment that you have or are going to invest in. For example, foam can be shaped, carved, and textured to resemble various materials, while thermoplastics can be molded and heat-formed for more intricate designs. It’s better to work with foam if you don’t have the heating equipment on-hand. Below is a quick list of each of the mentioned materials above and how to work with them.
- EVA Foam: Crafting cosplay armor with EVA foam entails creating templates, cutting and shaping the foam, then assembling the pieces with adhesive (usually white glue or mod podge). After refining the edges and adding details, the armor is primed, painted, and sealed for a polished appearance.
- Thermoplastics: Thermoplastics are generally plastics which can be heated to allow you to mold, stretch, or bend it for shaping. These are great for cosplay armor which calls for a metal or glass look to it. Some examples of thermoplastics are Worbla and Wonderflex. Working with thermoplastics, however, will need the use of a heat gun, molds, and soldering iron in some cases. Once the material has been heated and is already pliable enough, you may put it above the template or the mold for shaping prior to cooling, and adding the necessary details like texture. Afterwards, you can assemble the armor and painting, and finished off by sealing.
- 3D Printing: Creating cosplay armor through 3D printing starts with designing or finding a 3D model, slicing it for printing, then assembling and post-processing the printed pieces for a smooth finish. Once assembled, priming, painting, and sealing the armor bring it to life, while adding fittings and adjustments ensures a comfortable and captivating final look for your cosplay. 3D printing offers precision but demands patience in post-processing for a polished result, so refining printing techniques and settings is key to achieving intricate armor designs.
You might think that the creation period itself is the most time-consuming, and you would be right, but if you spend more time in the planning process, it will help lessen the effort and hours that you would spend during creation. As Einstein said before, “If I had an hour to solve a problem I’d spend 55 minutes thinking about the problem and five minutes thinking about solutions.”
2. The Creation Process Itself
Now that you’ve wrapped up the planning part, it’s time to translate your vision into reality. Gather your equipment, chosen materials, and design pegs, and start working.
When you’ve mainly chosen to work with foam, techniques like heat shaping, layering, and sculpting can help achieve some dimensionality and texture. After shaping the foam, you can apply a flexible coating for added durability. Painting techniques like dry brushing and weathering add some realism to your costume.
Thermoplastics, while pricey, are great materials to work with if you have the “thermo” part covered. You just need to heat the material until it becomes pliable, allowing you to mold and shape it over forms or directly onto a mannequin. The material’s malleability makes it ideal for forming complex curves and intricate details. Once shaped, you can sand, carve, and paint the thermoplastic to create realistic textures and finishes.
For the most intricate designs and builds, 3D printing is available, but this will be significantly pricier and is not advisable if you’re just starting out. You can use various filament types for different textures, and post-processing techniques like sanding, priming, and painting can bring the printed pieces to life.
Since armor is usually metallic in quality, metallic paints such as metallic acrylics and spray paints can be layered to mimic the appearance of metal. Moreover, weathering techniques, like dry brushing, rust effects, and chipping can add a worn and battle-hardened look to the costume.
3. Showing off your work
After all the hours, sweat, and tears that you spent in the creation of your costume, it’s now time to wear it and show it off to the event or shoot! We won’t really have much more to say about this part except this: be proud and have fun!